Machining of Medical Forging Tools
Manufacturer of medical forging tools: excellent know-how
At FORGINAL Medical, we offer the medical industry our expertise in the manufacture of specialized forging tools for the production of medical implants, particularly orthopedic and hip implants. We have taken the strategic decision to manufacture all our tools in-house. This approach enables us not only to guarantee total control over the quality and precision of our forged parts, but also to reduce production times and ensure complete traceability of the process.
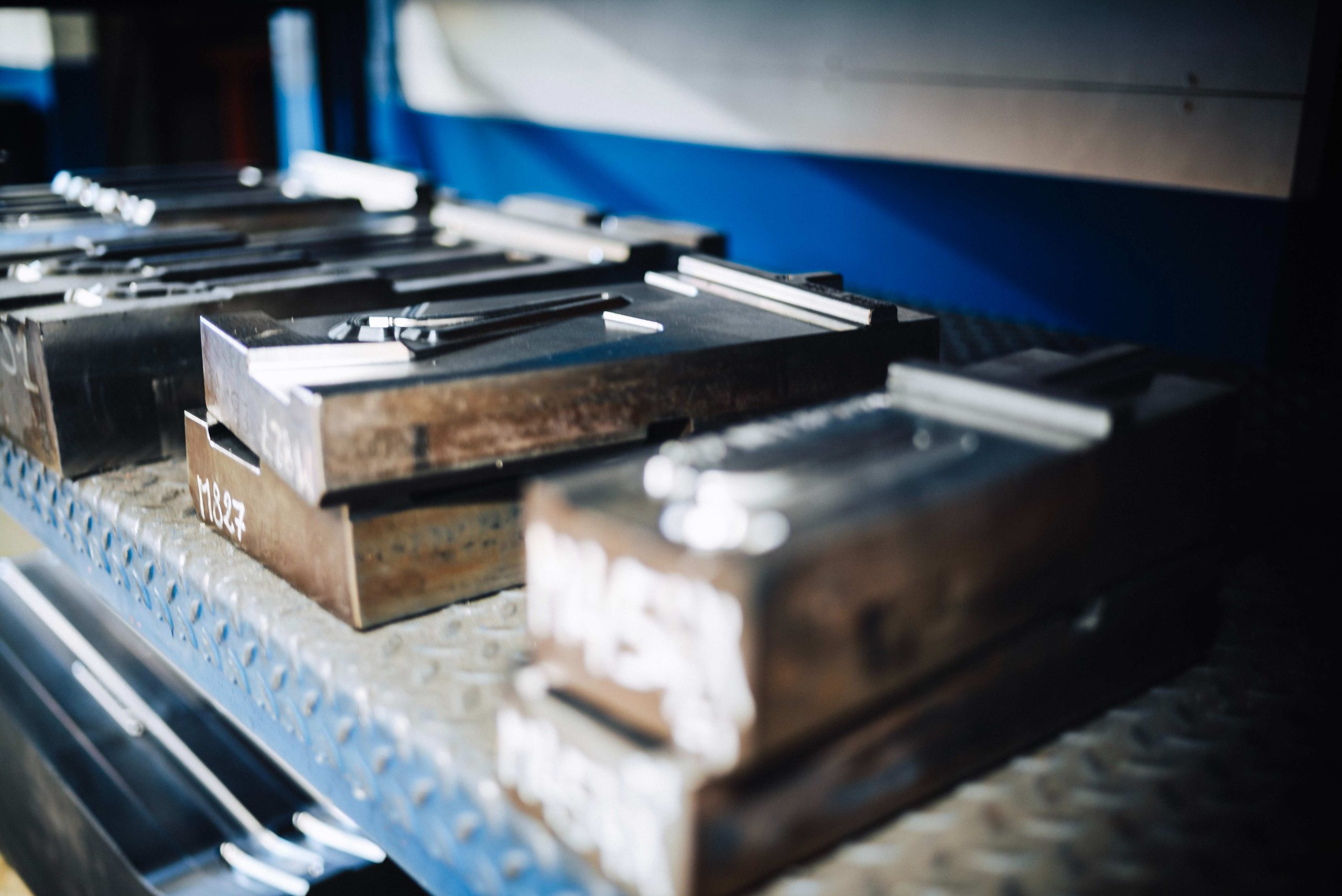
Machining: A Key Element of Implant Manufacturing
Machining tools for forging medical implants is a fundamental part of our expertise. With state-of-the-art equipment and a team of experienced engineers.
Tools Tailored to the Specific Needs of Each Implant
One of the reasons we favor in-house machining is the ability to tailor each tool to the specific needs of the implant. This includes creating specialized tools, such as those for post-printing parts or those for complex implants.
The Importance of Tool Quality in Ensuring Implant Precision
The forging tools we manufacture ensure optimal repeatability of the production process. Indeed, each forged part, whether an orthopedic implant or a hip prosthesis, must meet extremely strict dimensional tolerances. The quality of the tool directly impacts the precision of the forging process, the mechanical strength, and the durability of the implant. This is why at FORGINAL Medical, we take great care in designing and manufacturing our medical forging tools with maximum precision.
An Integrated Manufacturing Process for Optimized Results
Forging Tool Manufacturing: From Design to Machining
The manufacturing process of forging tools at FORGINAL Medical is entirely integrated and done in-house, allowing us to control every stage of production. From tool design to final machining, we take a methodical approach aimed at eliminating any possibility of manufacturing defects. Our engineers analyze each part to optimize production steps, reduce defects, and improve the forging processes.
Machining of Close-Form Parts
In the machining of forging tools, it is essential to consider close-form parts that require high precision. This is particularly important for post-printing parts with strict dimensional requirements. These parts must be machined carefully to ensure they meet the highest quality standards.
Bending Tool Manufacturing: For Complex-Shaped Implants
Bending tools play a crucial role in the manufacturing of hip prostheses and other implants with complex shapes. At FORGINAL Medical, we design and manufacture these tools custom-made for each project. Our bending tools allow us to work the material with high precision while respecting the required tolerances for medical implants. Thanks to these tools, we can produce implants with impeccable quality and complex shapes without compromising on strength or safety.
High-Tech Equipment for Precision Machining
CNC Machining for High-Quality Parts
To ensure optimal precision, we use state-of-the-art CNC machining equipment. These high-tech tools allow us to create special tools tailored to specific implants and machine complex parts with great accuracy. CNC machining is particularly well-suited for medical devices, where every millimeter matters to ensure the safety and efficacy of medical implants.
Manufacturing of Tool Parts and Machining Jaws
Tool parts, such as machining jaws, are essential to ensure proper holding of the implants during finishing operations. We manufacture these jaws to ensure perfect fixation of parts throughout the production process. The jaws are made from superior-quality materials to guarantee their durability and effectiveness throughout the production cycle.
Rigorous Quality Control and Traceability
Systematic Quality Control to Ensure Tool Reliability
At FORGINAL Medical, each medical forging tool undergoes rigorous quality control before being put into production. We perform systematic dimensional checks to ensure that each part produced meets the strictest medical device requirements. Resistance and durability tests are also conducted to guarantee the reliability of each tool.
Complete Traceability for Every Manufactured Tool
Traceability is a key element of our manufacturing process. This not only allows us to ensure consistent quality but also guarantees that each implant or hip prosthesis complies with current standards.
Recognized Expertise in the Manufacturing of Tools for Medical Implants
Thanks to our 100% integrated manufacturing process and decades of expertise, FORGINAL Medical stands as a leader in the production of tools for medical implant manufacturing. Our medical forging tools are designed to deliver results with extreme precision and are used to produce the highest quality orthopedic implants. We are committed to providing innovative machining solutions while ensuring the safety and performance of implants for the well-being of patients.