Implantable Titanium and Stainless Steel Plates
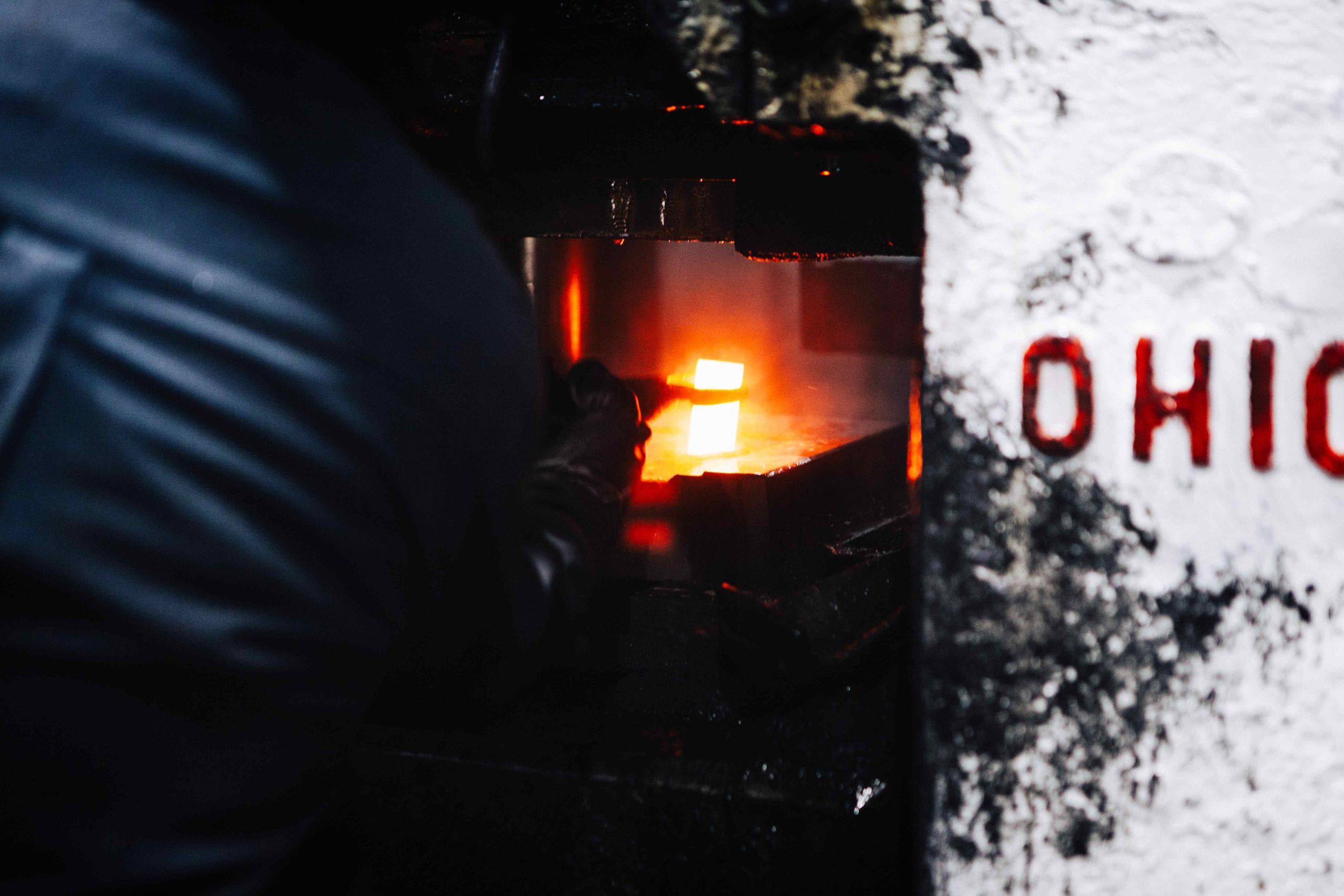
Forginal Medical: Manufacturer of Implantable Titanium and Stainless Steel Plates
In the medical field, precision, safety, and durability of implants are essential criteria for the success of surgical procedures. Orthopedic implants, particularly implantable plates, play a crucial role in bone fracture repair, fixation of complex fractures, and stabilization of damaged joints.
Forginal Medical, a leading player in the forging of medical-grade titanium and stainless steel parts, stands out for its unique expertise and ability to provide innovative solutions that meet the needs of healthcare professionals.
With recognized expertise in the manufacturing of high-quality implants, Forginal Medical offers products that meet the highest standards of performance and safety. This article explores Forginal Medical’s role in implantable plate manufacturing, the materials used, the production processes, and the applications of orthopedic implants while addressing frequently asked questions about these medical devices.
What Is an Orthopedic Implant?
An orthopedic implant is a medical device used to replace or support a part of the human body, usually a bone or joint. These implants are used in various surgical procedures, such as joint replacement, fracture fixation, or the repair of damaged bone tissue.
Orthopedic implants can be made from various materials, including titanium, stainless steel, and other specialized alloys, chosen for their mechanical properties and biocompatibility.
These devices are essential for restoring joint and limb function while reducing pain and accelerating patient recovery.
Forginal Medical’s Role in the Manufacturing of Implantable Plates
Expertise and Know-How
Forginal Medical is a company specializing in precision forging for the medical sector, with a particular focus on implantable plates. With decades of experience, the company has developed unique expertise in manufacturing complex medical devices.
The company’s expertise is based on a thorough mastery of high-precision forging processes, enabling the creation of implantable plates of various sizes with specific anatomical shapes. Each stage of production undergoes strict control to ensure that the implants are strong, durable, and perfectly suited to the needs of surgeons and patients.
Precision Forging for Implantable Plates
Implantable plates are very thin metallic components, often designed to conform to the shape of the treated bone. Their manufacturing requires particular expertise, as these plates must adhere to extremely fine tolerances and maintain perfect uniformity to ensure mechanical strength.
Forginal Medical uses advanced precision forging techniques to produce these implants. The process begins with raw material blocks, typically titanium or stainless steel, which are heated and shaped under extremely high pressure to achieve the exact shape and dimensions of the implantable plates.
Forging maintains a homogeneous metal structure, reducing the risk of deformation or breakage during implantation. The precision of this process is critical for patient safety and ensures the optimal performance of the medical device. Forginal Medical’s ability to manufacture thin, strong, and anatomically adapted implantable plates is one of its key strengths.
Materials Used: Titanium and Stainless Steel
Titanium: The Preferred Material for Medical Implants
Titanium is a highly favored material in medical implant manufacturing, especially for implantable plates, due to its exceptional properties. It is extremely lightweight yet remarkably strong, making it an ideal choice for medical devices subjected to high mechanical stress.
Titanium is also highly resistant to corrosion, allowing implants to withstand the harsh environment of the human body for many years. Additionally, titanium is biocompatible, meaning it is well tolerated by the body without causing rejection or inflammatory reactions.
These properties make titanium a top choice for orthopedic implants, particularly plates used for repairing complex fractures or stabilizing fragile bone structures.
Stainless Steel: Strength and Durability
Stainless steel is another commonly used material for orthopedic implants, including plates and screws. It is characterized by high mechanical strength and excellent durability, in addition to being relatively easy to machine.
The mechanical properties of stainless steel make it an ideal choice for applications requiring implants capable of withstanding heavy loads while maintaining high resistance to wear.
Its ability to withstand compressive forces and fatigue is crucial for implants that will be subjected to continuous mechanical stress throughout a patient’s life.
Applications of Implantable Plates
Hip Prostheses: A Typical Example of an Implantable Plate
Precision forging allows the manufacturing of hip prosthesis components with maximum strength and perfect adaptation to the patient’s bone structures.
A hip prosthesis must withstand considerable mechanical stress, reaching several tons per cm² during certain stages of rehabilitation. This is why implants must be designed and manufactured to endure these forces throughout the patient’s life.
Applications in Complex Fractures and Bone Stabilization
Beyond hip prostheses, implantable plates are also used to treat complex fractures or bone deformities. These plates help maintain proper bone positioning, promoting quick and optimal fracture healing.
Whether for repairing spinal fractures, femoral fractures, tibial fractures, or other areas of the body, implantable plates play a crucial role in restoring bone function.
Manufacturing Process of Implantable Plates
Precision Forging: Ensuring Thinness and Strength
The manufacturing of titanium or stainless steel implantable plates begins with precision forging. This process transforms a raw metal rod into a precisely dimensioned plate while ensuring perfect material uniformity.
This stage is critical, as implantable plates must be extremely thin, posing a significant technical challenge. Forging allows for this thinness while maintaining maximum mechanical strength.
Finishing and Quality Control
Once forged, the plate undergoes finishing steps to ensure it meets the strict tolerances of the medical industry. Forginal Medical uses advanced contouring techniques to prevent the risk of breakage or deformation of the piece.
Contouring is preferred over traditional cutting because it results in smooth, flawless edges, which are essential for the implant’s proper function within the human body.
Each implantable plate undergoes rigorous quality control before being shipped, ensuring compliance with the strictest safety standards. Tests include mechanical strength assessments, biocompatibility evaluations, and performance checks to guarantee that each product meets the expectations of surgeons and patients.
Conclusion: Forginal Medical, a Trusted Partner
Thanks to its unique expertise in precision forging and its expertise in the use of materials such as titanium and stainless steel, the company strives to produce orthopedic implants that offer exceptional strength, maximum biocompatibility, and perfect adaptation to patient needs. With advanced production capabilities, rigorous manufacturing processes, and a constant focus on innovation, Forginal Medical is a trusted partner for medical professionals, guaranteeing safe and high-performance implants for the treatment of fractures and orthopedic conditions.