Mastery of Requirements
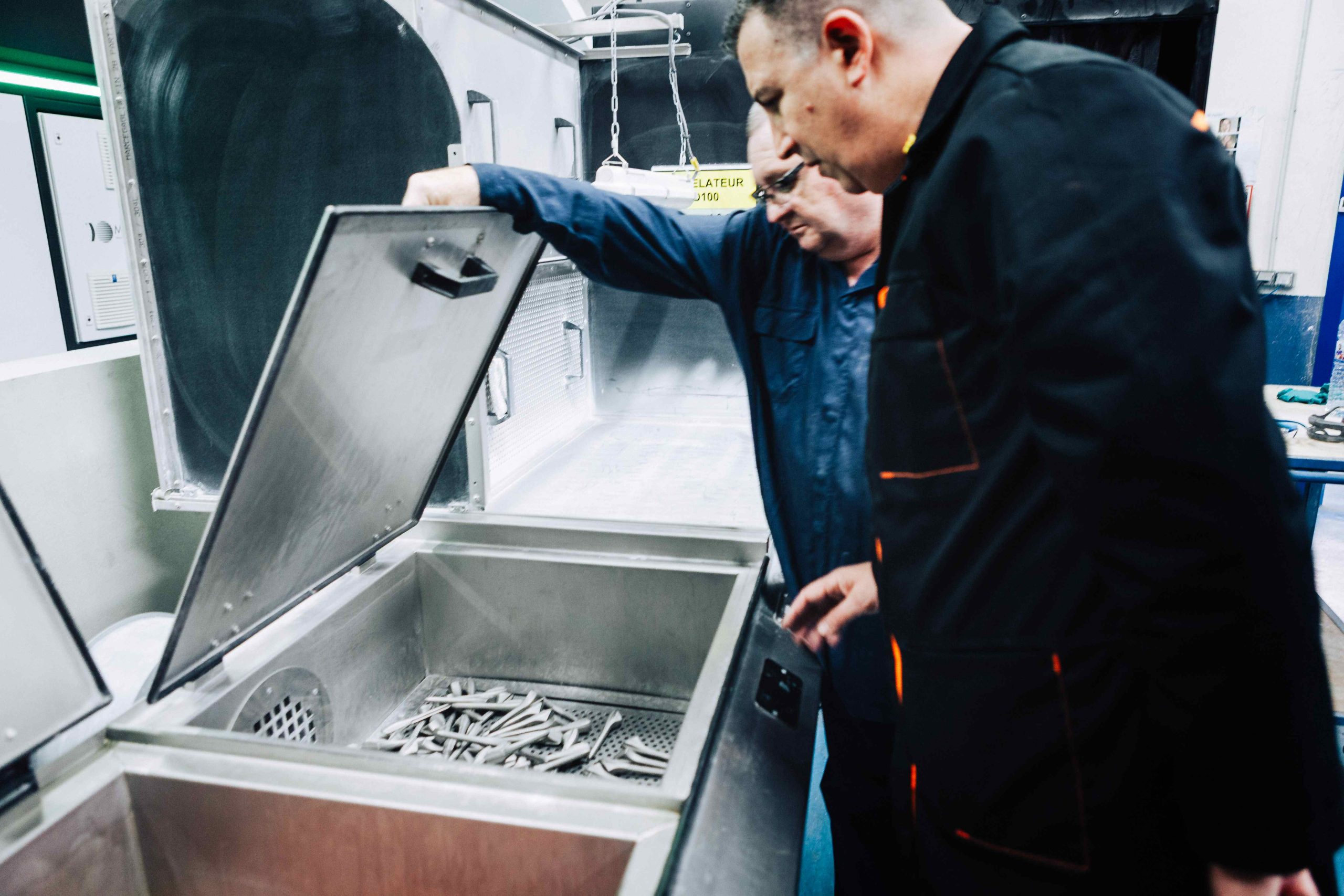
A Strong Commitment to Quality
Forginal Medical stands out for its ability to meet the most stringent requirements in medical implant manufacturing. Over the years, the company has acquired unique expertise in producing components for the medical sector, particularly orthopedic implants. We are committed to maintaining exceptional quality standards, ensuring reliable, durable, and safe products for patients. Thanks to our technical expertise and mastery of manufacturing processes, we can meet even the most complex needs of the medical industry.
Manufacturing Process: Expertise That Meets the Highest Standards
The Role of Tolerances and Precision
Mastering quality requirements involves a strong focus on precision and tolerances in production. At Forginal Medical, we have integrated rigorous processes to achieve extreme precision.
The production of medical implants requires extremely tight tolerances, far exceeding standard industrial benchmarks. Thanks to state-of-the-art forging and machining equipment, we ensure manufacturing precision that minimizes failure risks and guarantees long-term implant performance.
Mastery of Forging Processes
The manufacturing process at Forginal Medical is based on expertise in forging and high-precision manufacturing techniques. We have chosen to use power hammers for forging our components because this method allows for finer and more precise control of the shapes and dimensions of implants. Unlike presses, which apply uniform pressure across the entire piece, power hammers enable more customized shaping, reducing the risks of deformations or material weaknesses.
We have mastered 95% of implantable titanium and 5% of implantable medical stainless steel in our productions. This expertise in forging implantable materials ensures exceptional reliability and durability of the produced implants. Titanium is particularly valued for its corrosion resistance and mechanical properties, making it ideal for use in demanding environments such as the human body.
Quality at the Heart of Innovation: Manufacturing Control
Rigorous Quality Control
The quality of each medical implant is verified at every stage of the manufacturing process. Quality control is, therefore, an essential process at Forginal Medical. Each component undergoes a series of rigorous tests before being approved for medical use. From material selection to final inspection, we ensure that every implant meets strict performance and safety standards.
Our quality control tests include mechanical strength analysis, biocompatibility testing, and corrosion resistance assessments. We rely on high-precision measurement tools to guarantee that all components meet strict dimensional and performance criteria. The materials used are tested for their durability and ability to withstand conditions inside the human body while maintaining long-term reliability.
Engineering and Design Simulation
The Forginal Medical engineering department plays a key role in ensuring product quality. Using advanced design software such as SolidWorks, we model and simulate each implant before production. This allows us to detect potential design anomalies before manufacturing, reducing the risk of errors and non-compliance.
Our simulation tools also include virtual tests to validate the mechanical performance and resistance of implants under various physiological conditions, considering the exact specifications of orthopedic implants. We also use Mastercam, a machining and design software, to create precise manufacturing programs, especially for implants with tight tolerances.
Specific Requirements for Medical Implants: Biocompatibility and Durability
Biocompatibility and Long-Term Performance
One of the main challenges in medical implant manufacturing is ensuring the biocompatibility of the materials used. Forginal Medical carefully selects materials suitable for medical applications, such as titanium and medical-grade stainless steel, which are known for their corrosion resistance, longevity, and smooth integration into the human body.
Orthopedic implants, whether titanium prosthetics or other devices, must not only withstand the biological conditions of the human body but also endure mechanical stresses. That is why we conduct durability tests on our components to ensure their long-term performance, reducing the need for replacements or maintenance.
Our materials are tested to ensure they effectively resist internal body environments, including temperature variations, humidity, and mechanical stresses. Titanium, for example, is highly valued for its corrosion resistance and exceptional mechanical properties, making it an ideal material for high-performance implants.
Compliance with International Standards
At Forginal Medical, we adhere to strict manufacturing requirements, complying with international standards for medical implant production. We follow frameworks such as ISO 13485, ensuring that our products meet the highest quality and safety criteria. Each stage of our manufacturing process is meticulously controlled to guarantee product reliability and compliance.
Our implants are designed to integrate seamlessly with human body requirements, minimizing the risk of rejection or post-operative complications.
Mastering the Requirements for Quality Medical Implants
We ensure reliable, durable and safe orthopaedic implants for patients, helping to improve medical care through an approach focused on quality, performance and safety. Whether it’s titanium prostheses, stainless steel implants or other medical solutions, Forginal Medical is the trusted partner to meet the challenges of the medical implant industry.